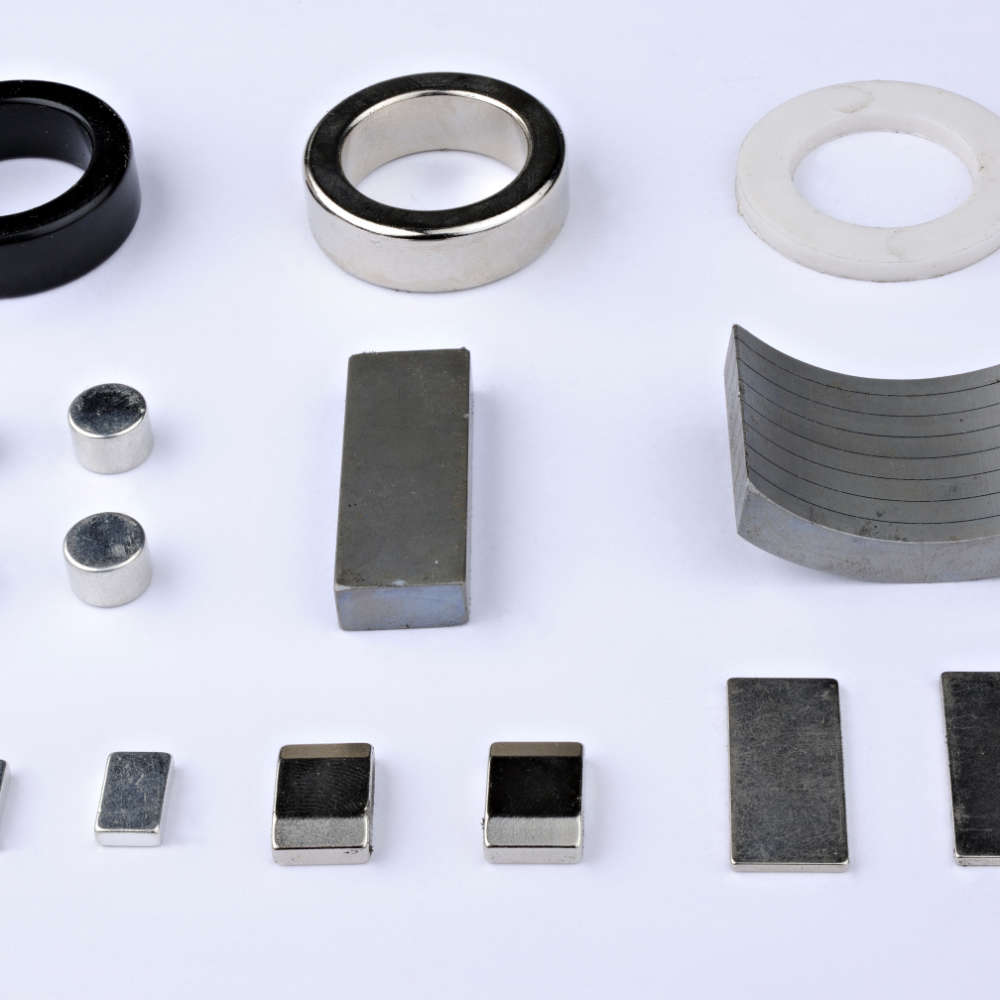
Magnets Neodymium Sintered
The material for high adhesive force when it has to be small.
Due to their high adhesive force and small volume, magnets made of neodymium enable new technical solutions. Despite using less material, the system performance remains the same compared to the other materials. Miniaturization enables new and innovative technical product and process solutions.
Features / Advantages
- Neodymium sintered magnets currently have highest magnetic strength
- High magnetic stability
Application areas
Neodymium magnets have a wide range of applications, so that only a few examples of use can be mentioned here:
- Electric, servo, DC, synchronous and linear motors
- Generators
- Central rotary and spur rotary couplings
- Hysteresis and eddy current brakes
- Sensors
- Adhesive applications
- Actuators
Magnet production
For sintered magnets made of neodymium, neodymium, iron, boron, dysprosium and in small proportions other elements such as cobalt, copper, gallium and aluminum are used for as the base material.
The material is melted in a furnace at temperatures above 1300°C, poured into a mold and cooled in metal blocks. The blocks are pulverized and ground to approx. 3µm small particles. In this phase, the small particles are in a magnetically anisotropic state. At temperatures above 725°C, the particles are pressed into shapes. In this phase, the blocks reach approx. 75%-80% of the theoretically maximum possible density. In the next step, sintering takes place under inert gas or vacuum for several hours at temperatures just below the melting temperature of the powder mixture, between 1030°C and 1100°C. At this temperature, the small particles in the powder adhere more strongly to each other, so that the blocks shrink to a density of 99% of the theoretically maximum possible density.
Following heat treatment at temperatures between 600°C and 900°C, the blocks are shaped into the desired form, receive a surface treatment and are magnetized.
Magnet shapes
The most commonly used magnet shapes are cuboids, rings, cylinders and segments. Separation technology also makes it possible to obtain miniature magnets from the magnetic blocks.
For other molds, the shape must be determined before pressing. Otherwise, the subsequent adjustment of the shape from the magnetic blocks is too complicated and expensive. Likewise, bevels, countersinks, holes, notches, etc. can only be made in the pressing direction. For anisotropic magnets, these are only possible at right angles to the preferred direction.
Temperature behavior
Although the maximum possible operating temperature for NdFeB magnets is between 80°C and 220°C depending on the material, it depends on the position of the operating point. This is determined by the shear of the passive magnetic circuit and the opposing field loads that occur. If the operating point remains within the linear range of the demagnetization characteristic, no irreversible demagnetization phenomena occur. If the so-called buckling field strength, from which the demagnetization characteristic no longer runs linearly, is exceeded, demagnetization occurs. This can be remedied by remagnetizing.
Chemical and mechanical properties
Due to their chemical composition (high iron content), sintered NdFeB magnets and their crystal structure are very susceptible to environmental influences. For this reason, Tridelta offers all grades alternatively as a low-corrosion material. In this process, part of the iron content is replaced by cobalt and other metals, so that the tendency to corrosion is significantly reduced.
Alternatively, Tridelta also offers all types of surface coatings so that harmful environmental influences can be prevented.
Please select the desired coating from these alternatives when making your inquiry:
- Electroplating with Ni, Cu, Sn, Zn, Al, Ag or combinations
- Epoxy resin as spray painting or as electrodeposition painting
- Parylene coating
- PTFE coated magnets
Magnetic properties
Neodymium magnets are currently the strongest permanent magnets. The advantage of neodymium magnets is their high adhesive force with small volume, which they do not lose even after many years.
REFeB 263 / 96 |
N35 | 263 | 1,17 | 868 | 955 | 1,05 | 80 | -0,11 | -0,6 |
REFeB 287 / 96 |
N38 | 287 | 1,22 | 899 | 955 | 1,05 | 80 | -0,11 | -0,6 |
REFeB 342 / 96 |
N45 | 342 | 1,32 | 923 | 955 | 1,05 | 80 | -0,11 | -0,6 |
REFeB 382 / 88 |
N50 | 382 | 1,4 | 796 | 875 | 1,05 | 80 | -0,11 | -0,6 |
REFeB 263 / 112 |
N35M | 263 | 1,17 | 868 | 1115 | 1,05 | 100 | -0,10 | -0,6 |
REFeB 287 / 112 |
N38M | 287 | 1,22 | 899 | 1115 | 1,05 | 100 | -0,10 | -0,6 |
REFeB 318 / 112 |
N42M | 318 | 1,28 | 955 | 1115 | 1,05 | 100 | -0,10 | -0,6 |
REFeB 342 / 112 |
N45M | 342 | 1,32 | 995 | 1115 | 1,05 | 100 | -0,10 | -0,6 |
REFeB 263 / 135 |
N35H | 263 | 1,17 | 868 | 1350 | 1,05 | 120 | -0,10 | -0,56 |
REFeB 287 / 135 |
N38H | 287 | 1,22 | 899 | 1350 | 1,05 | 120 | -0,10 | -0,56 |
1) Designation based on DIN 17410/IEC 60404-8-1
2) The maximum possible operating temperature depends on the dimensioning of the system.