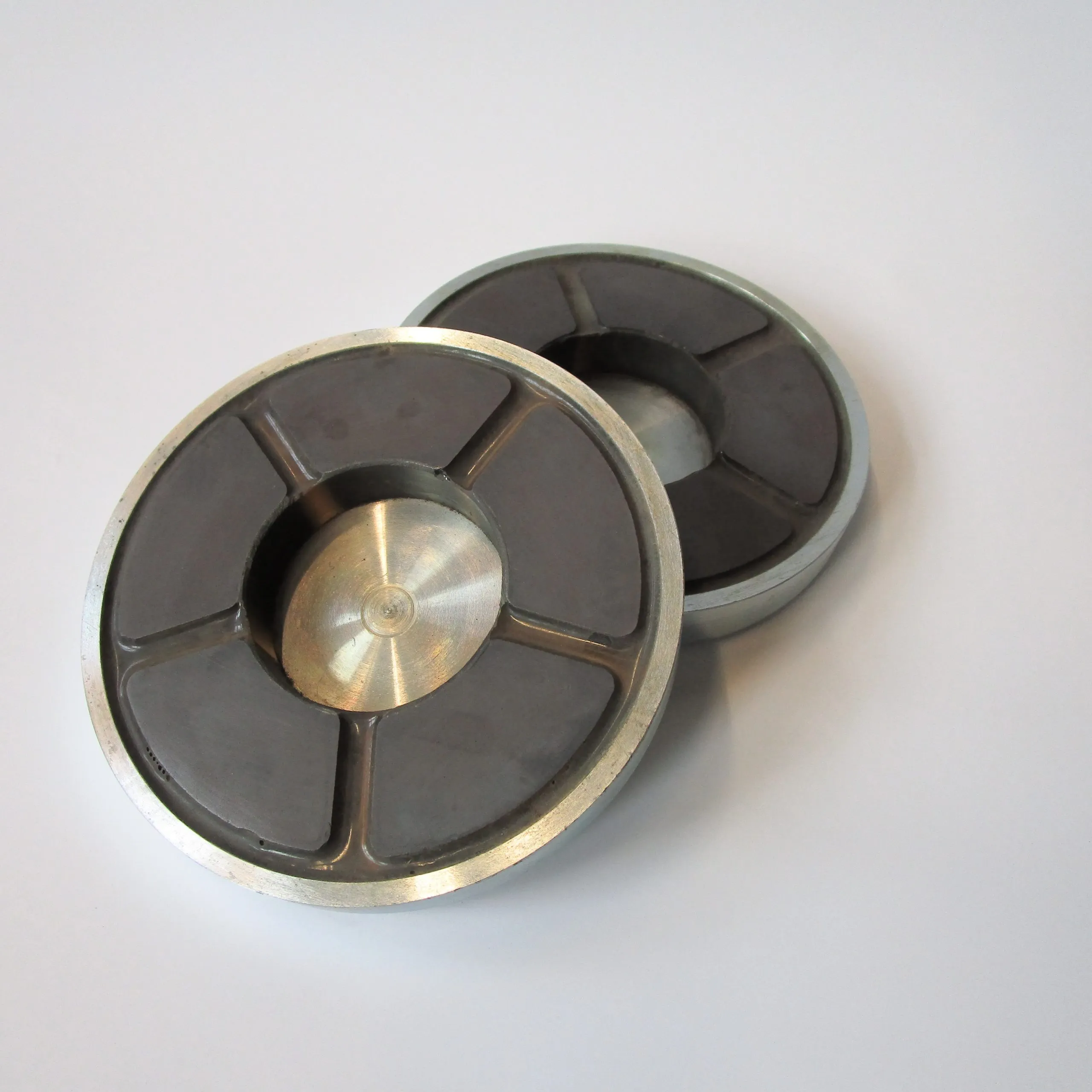
Spur Rotary Coupling
The spur rotary coupling transmits a high torque with little installation space.
The special feature of the face swivel clutch is the friction-free transmission of torque even with axial center offset or tilting.
Application area
Face rotary clutches are used in applications where rotary energy needs to be transmitted through walls without contact, vibration, noise and wear.
Exemplary areas of application
- Screw-on systems for caps and bottle closures
- Pumps for liquids and gases
Exemplary industrial sectors
- Food
- Chemistry and pharmacy
- Medicine
- Wind energy
- Special mechanical engineering
- Plastics industry
Features/Advantages
- wear-free, since contactless
- currentless, which means: fail-safe, low-maintenance, sustainable
- no follow-up costs
- Transmits forces vibration-free
- noiseless
Versions spur rotary coupling
Permanent magnetic face rotary clutch
is offered by Tridelta as standard with torques of up to 35 Nm. In addition, we can develop and implement customer-specific solutions.
The clutch halves of the face swivel clutches with neodymium magnets (samarium-cobalt magnets as a special design) are supplied mounted in an iron return. The hole in the iron socket can be specified when ordering and is made individually by Tridelta. It is also possible to purchase them undrilled and drill the holes yourself. Thanks to the very strong neodymium-iron-boron magnets, an axial center offset of 5 mm and a deviation of parallelism of 2-3° can be allowed without significant torque losses.
Face swivel couplings made of hard ferrite can be graduated more finely. When using neodymium or samarium-cobalt magnets, higher torques can be achieved in a smaller installation space.
Functionality spur rotary coupling
With the face rotary clutch, two magnetic disks with the same number of magnetic poles face each other in mirror symmetry. This coupling utilizes the attractive and repulsive properties of the magnetic poles: When one disk is rotated, the other disk moves with it due to the magnetic force of attraction. As soon as a resistance to rotation is exceeded on the output side, the clutch slips. It then forwards only a residual amount of the force.
The limitation of this torque is determined by the following factors:
- the distance between the magnetic disks (air gap)
- the material of the magnetic discs
- the number of magnetic poles on the magnetic disks
- the size of the magnetic disk surfaces
- the operating temperature
Temperature behavior of the magnets
The operating range of ferrite and neodymium magnetic couplings is between -30 °C and +100 °C. With increased or decreased operating temperature, the transmittable torques decrease or increase. For samarium-cobalt magnets, the operating range is between -190 °C and +250 °C. The respective coupling returns to its initial values at room temperature.
If an electrically conductive partition wall is used between the two magnetic disks, eddy currents are induced in the wall. This leads to eddy current losses, which reduce the maximum clutch torque depending on the speed. In addition, the eddy currents generate heat losses in the slit workpiece, which is why cooling may be necessary. The additional eddy current losses must be compensated for by the drive, so that the motor must be dimensioned larger by this loss component.