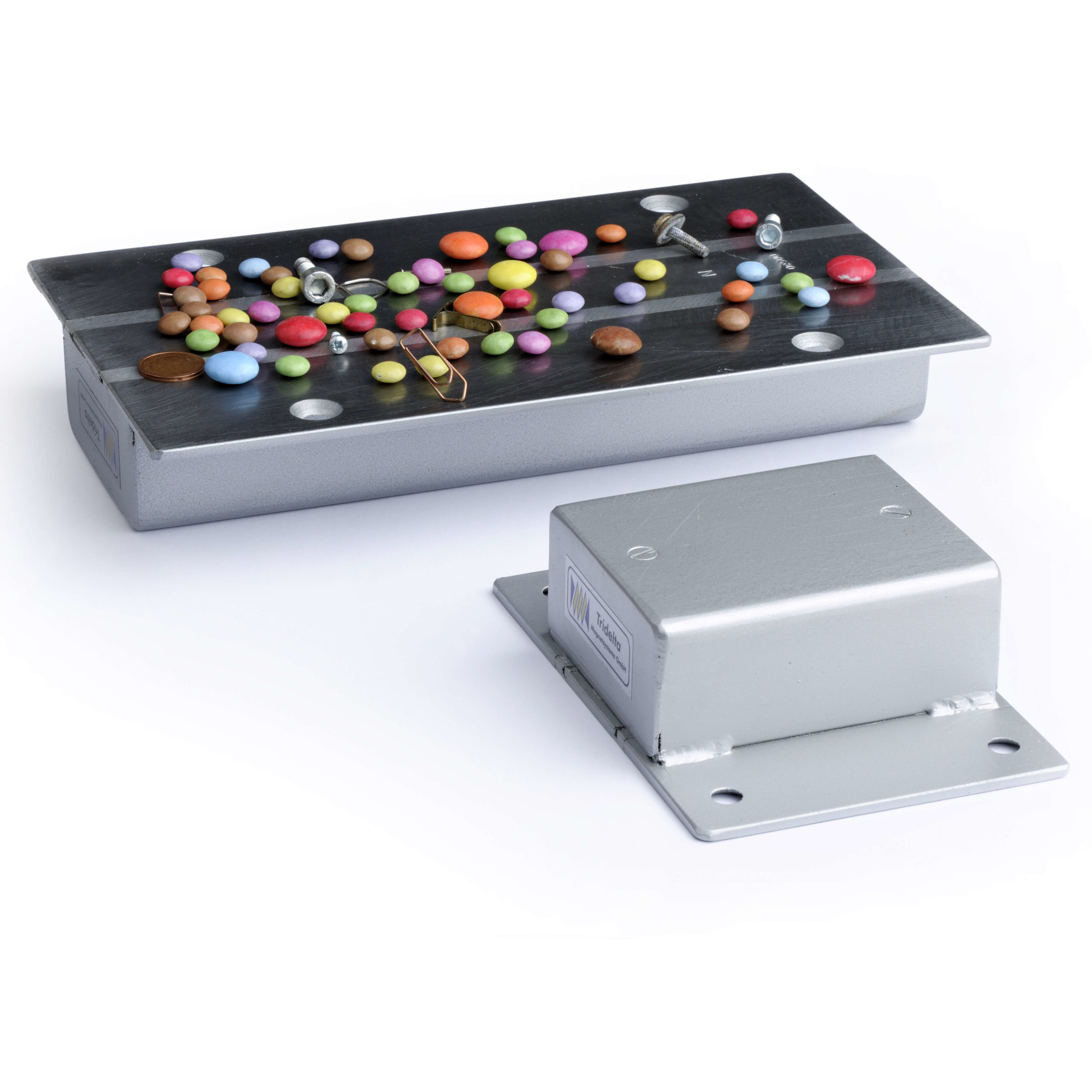
Plate magnets
Finding the needle in the haystack.
Plate magnets enable an uninterrupted flow of material. They operate without power, are fail-safe, low-maintenance, sustainable and do not incur any follow-up costs. In addition, this type of magnet can also be subsequently integrated into an existing process.
Application Plate Magnets
Flat separators are ideal when magnetic parts have to be separated from conveyable products such as wood and metal chips, powders, highly viscous liquids, etc., or other goods have to be cleaned of magnetic parts during the running process. For this purpose, they are mounted, for example, above or below conveyor belts, chutes, vibrating tables and filling hoppers.
In the plastics industry, magnetic separators clean pulverized starting material. They are also used to clean the pulp in the paper industry. They can also be used for the removal of ferromagnetic particles from floors in factory halls, from parking lots, airfields, horse show grounds, etc.
Tridelta flat separators can be permanently installed in existing plants. At the installation site, the material to be sorted should have the lowest migration rate and the lowest layer height.
Versions plate magnets
With flat separators, a distinction must be made between what they are to be used for and what material is to be separated. Tridelta manufactures two types of flat separators:
Embodiment I | Embodiment II | |
magnetic flux density | > 480 mT resp. > 1150 mT | > 360 mT |
Catch height | 30 – 60 mm | 55 – 120 mm |
Functionality plate magnets
Flat separators consist of a magnet system surrounded by a welded housing. Removing the catch from the magnet is done by wiping it off with a safety glove. Alternatively, Tridelta equips plate magnets with a cleaning device.
To allow the plate magnet to be retrofitted into existing systems, the housing is provided with mounting holes. To achieve larger catch areas, several magnets can be combined to form a catch unit.